PID Position Control System
The PID Position Control of a levitating balsa disc assembly inside a 500ml graduated cylinder is a system designed to teach the fundamentals of control of a fast responding positional system.
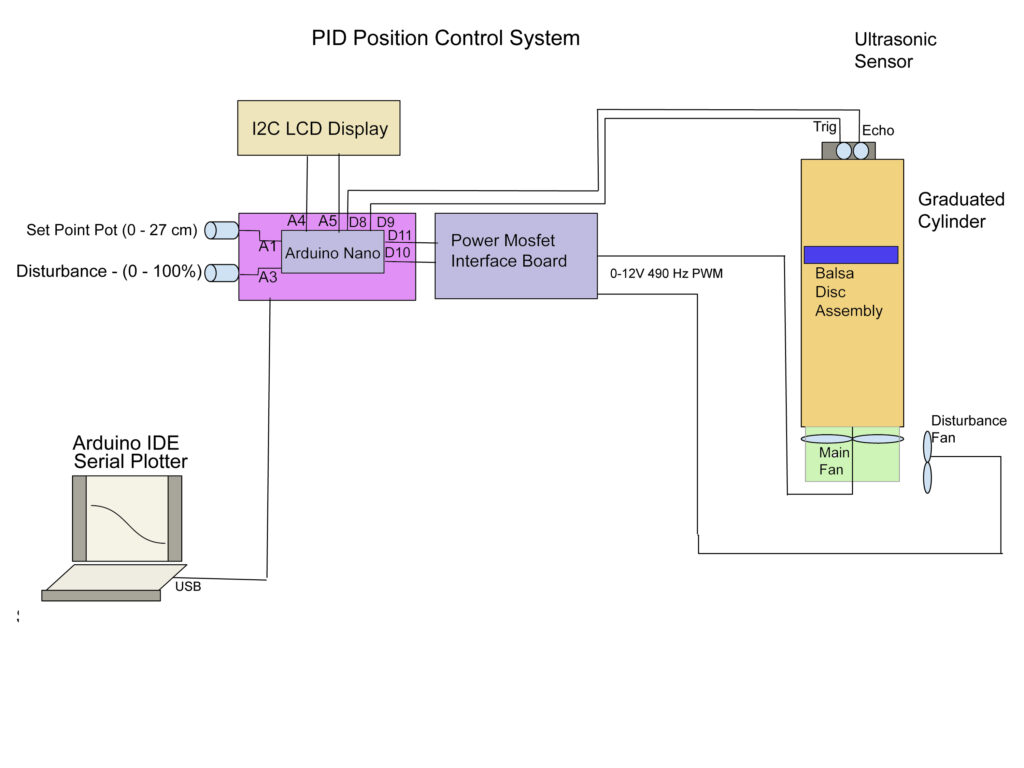
Project description
The PID Position Control of a levitating balsa disc assembly inside a 500ml graduated cylinder is a system designed for educational purposes . It complements the PID Temperature Control of a Miniature Thermal Chamber project in that it is a relatively fast responding process control system with very different process dynamics compared to the PID Temperature Control system. These differences will require very different PID tuning constants.
The system could be used as an inexpensive process control lab with many useful educational outcomes such as developing an understanding of process control and the effects of process dynamics on selecting the optimum PID (proportional, integral, and derivative) tuning constants. The lab would be suitable for students in electrical/electronics, mechanical, or chemical engineering / engineering technology .
The electronics for the PID Position Control System project and the PID Temperature Control of a Miniature Thermal Chamber project is the same . The IDE is the Arduino IDE and the serial plotter is used for both. Only the C code will differ.
The system hardware consists of a 500 ml plastic graduated cylinder with the bottom reamed out, a control board and an interface board , two 12 V DC fans , and an ultrasonic sensor . The balsa disc assembly is easily constructed using 4 pins and 2 45 mm discs cut using an exacto knife.
The interfacing board consists of an Arduino Nano , a setpoint potentiometer for setting desire position in cm and a disturbance potentiometer that adjusts the disturbance fan.. The outputs from the Nano are 2 pulse width modulated signals that produce a variable DC voltage that drives the 2 fans.
The interface board utilizes 2 N Channel power Mosfets and uses the PWM signals from the Nano to produce a PWM output with a maximum voltage of 12VDC to supply the ther2 fans.
The protytping board is supplied by PTSolns , a Calgary Canada based company.

PID Position Control System Components including:
500 ml graduated cyclinder, LCD display, interfacing board, air flow and disturbance fans, IR remote, balsa disc assembly, and the ultrasonic sensor assembly.
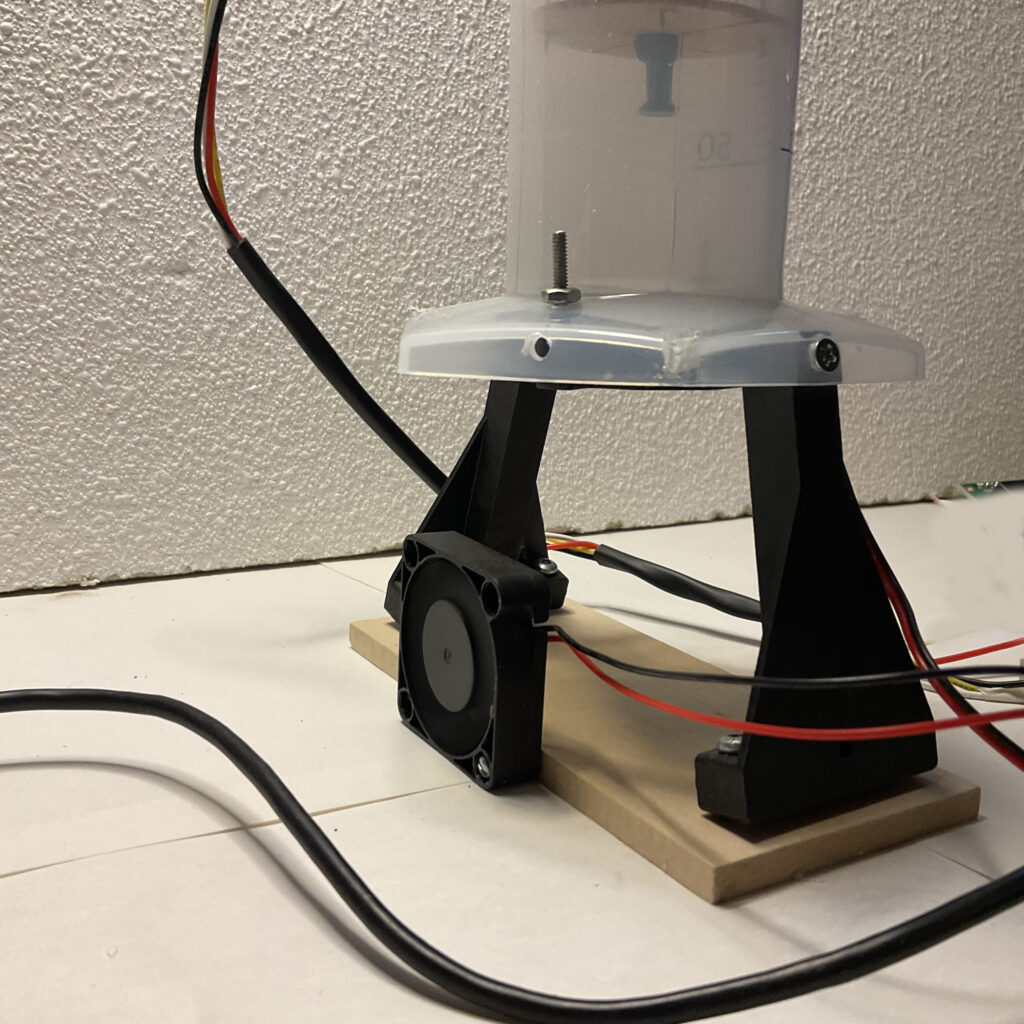
Disturbance fan and at the base of the cylinder is the main airflow fan.
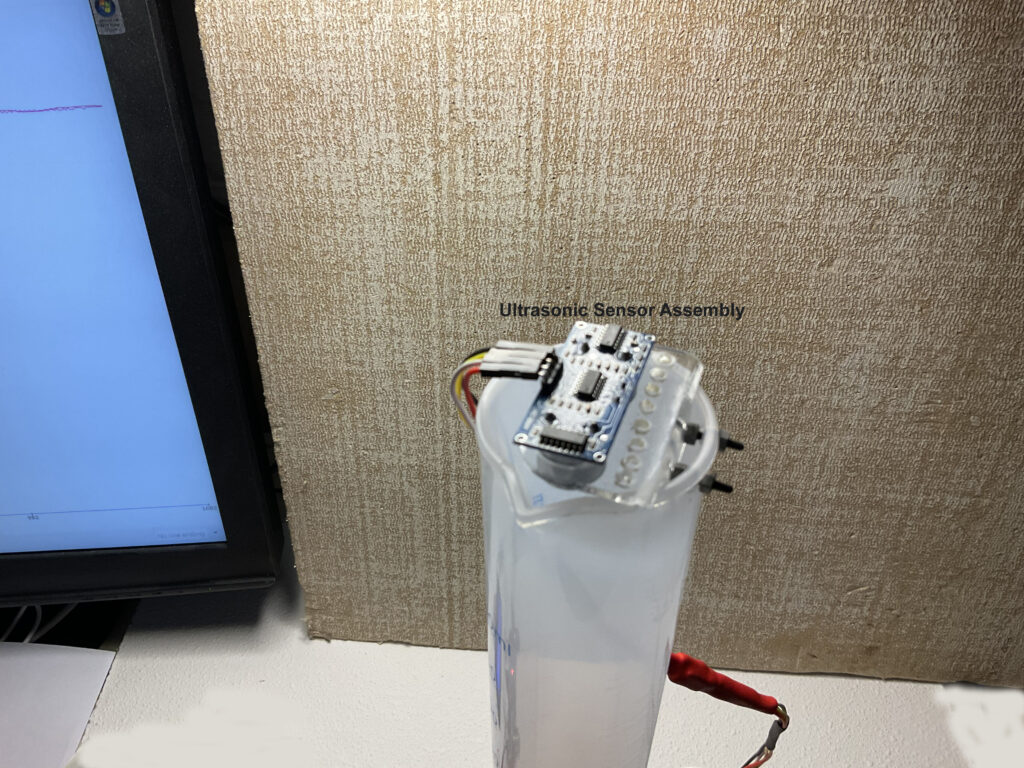
Ultrasonic sensor assembly
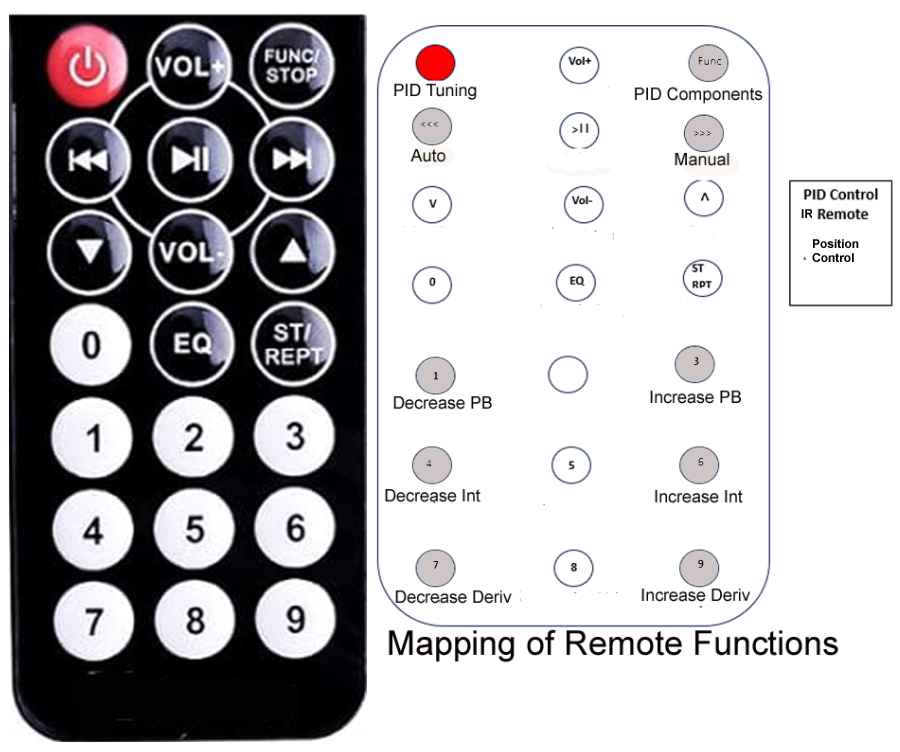
Infra Red Remote Mapping for PID Position Cotrol
Schematic Diagram
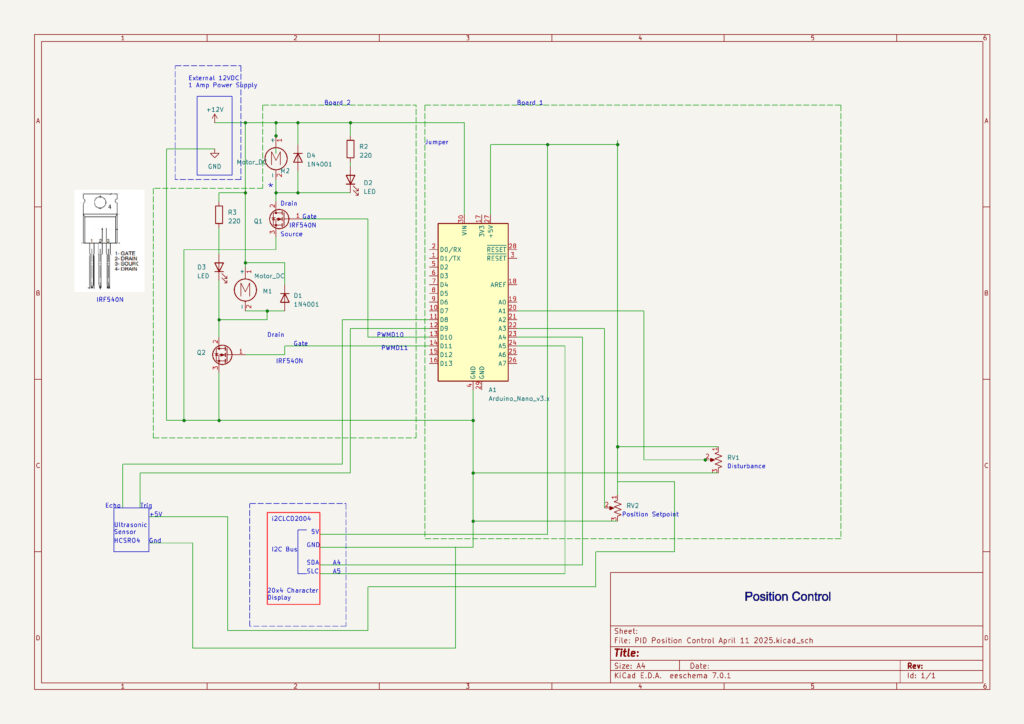
Connections to the Interfacing board
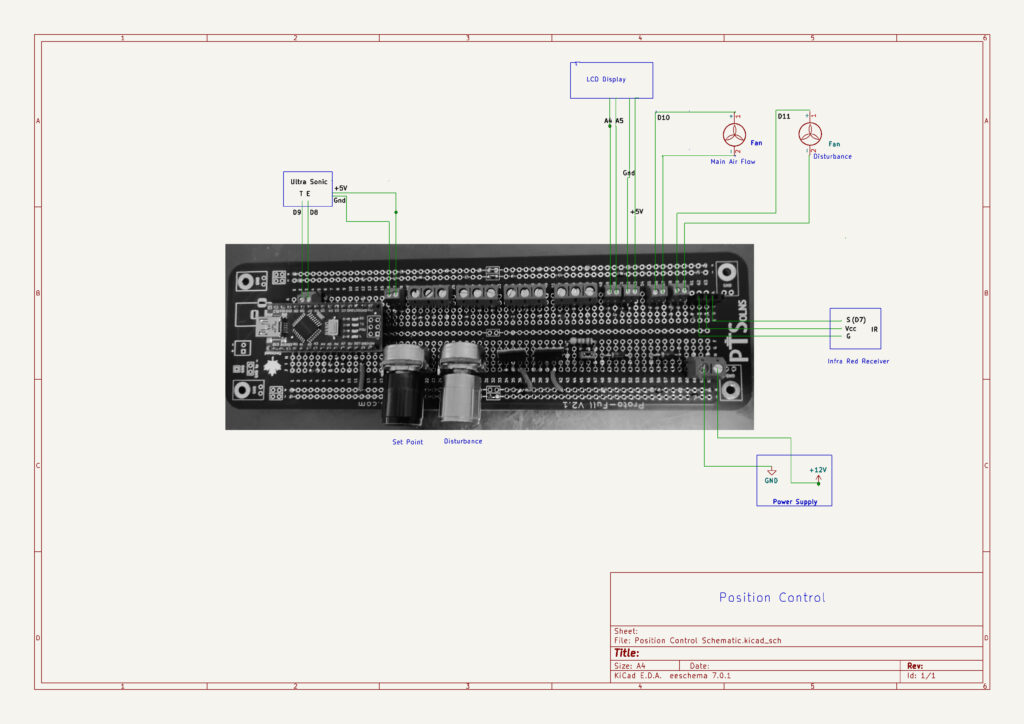
Point to point wiring for the interfacing board
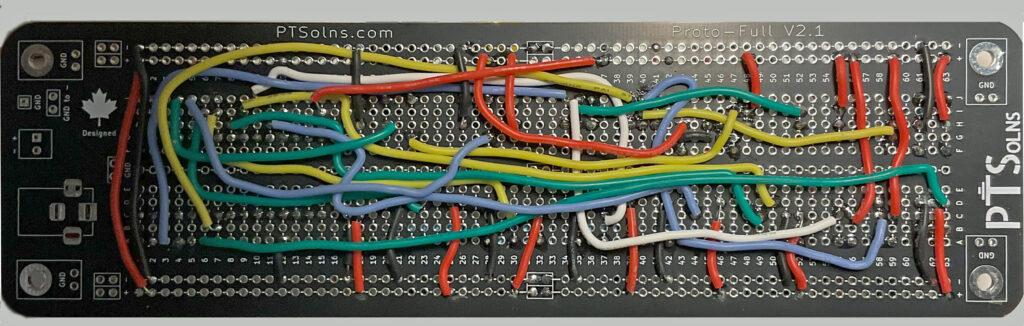
PID Position Control – Arduino C C++ Code
The following link is to a video of the position control system reacting to set point changes. The somewhat vibratory balsa disc assembly is due to the turbulent air flow. Some filtering of the ultrasonic position signal was required.